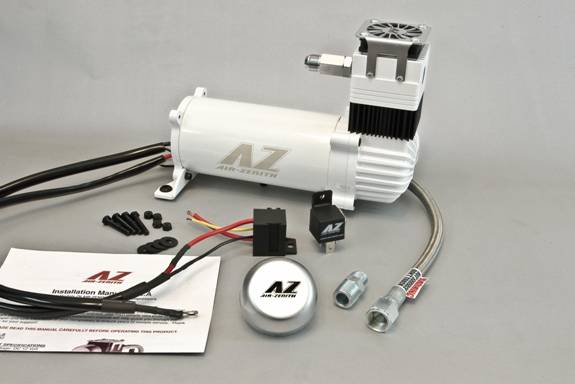
The OB2 compressor from Air Zenith redefines the OB line of compressors like the Hummer did to the off-road industry. Like the hummer Air Zenith engineers went back to the drawing board to look at every aspect of the OB1 compressor looking at both what made it so popular as well as those aspects that caused undesired operation.
Not a single compromise was made when re designing the flagship of the Air Zenith line. The OB2 compressor shares not a single part from its predecessor every single part when under intense scrutiny and analysis. Let me walk you through what, how, and the why the OB2 compressor is the fastest compressor you can buy.
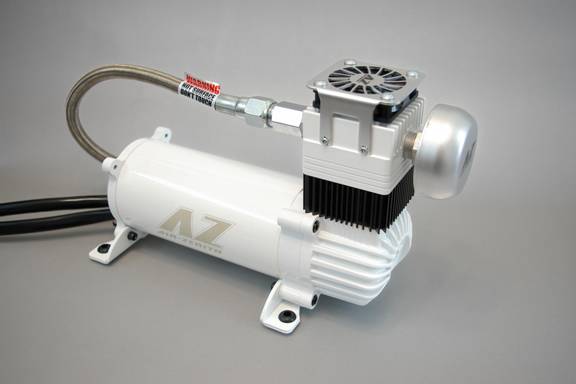
First impressions with the compressor you will notice the extreme weight of the compressor. For its size the compressor feels as though it is constructed of led. Every bit of the 19.05lbs of the compressor is due to the robustness of its design. The compressor in fact is made from 100% 6061T6 Aircraft grade aluminum. So this right away lets you know the body and mounts have all been beefed up to handle the stress and torture seen on today’s mini trucks. The heaviest part of the compressor is the drive assembly the 3/4HP motor that I will go into more detail later is a marvel of engineering. And last the extremely over built piston and rotating assembly has also been strengthened to handle the extreme stress of a high performance compressor.

Every aspect of the OB1 compressor where issues where found, months of research went into finding solutions to prevent problems from ever coming back. For example, the mounting system. The Ob1 compressor has thin small feet that where held to the compressor in a complex manor that required the user to dismantle the compressor when changing the orientation of the feet. On the OB2 the feet are now twice as thick and gusseted for strength.
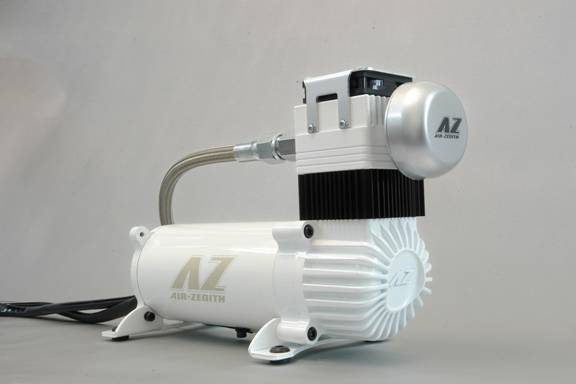
By far the best feature now is the feet can be oriented in the vertical or horizontal configuration without ever needing to remove any more then the (4) mounting bolts for the feet and simply rotating them to there desired position.
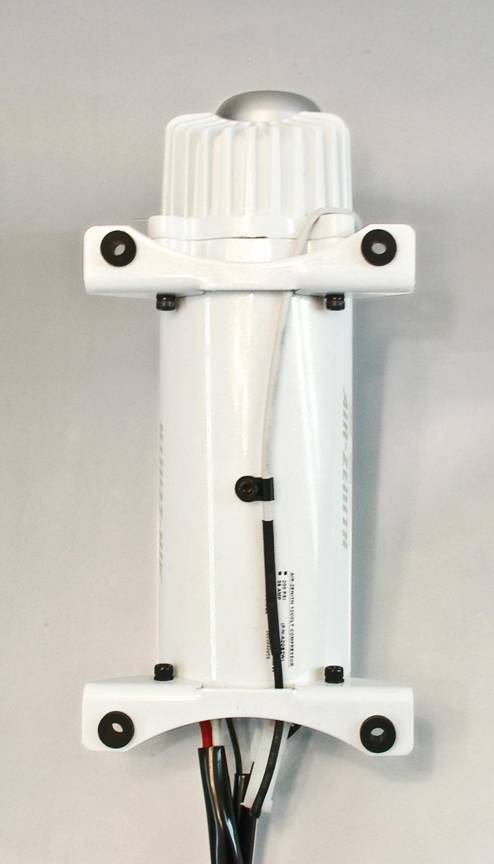
The head of the OB2 is now also twice as thick as the OB1 sporting fins now 4X thicker then the OB1 this prevents the fins from bending from impact as well as prevents small items from getting lodged into the fins and preventing adequate ventilation.
The crank case has also been structurally strengthened and converted to a one piece design to eliminate the possible sites of leaks.
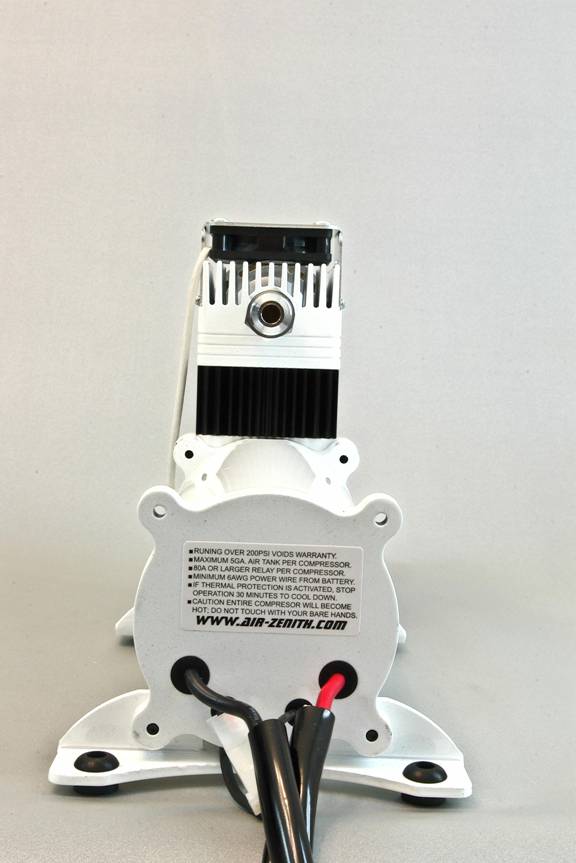
They key to any compressors operation is how it is wired. Allot of thought was put into the new design and how the compressor will be wired. For the first time from Air Zenith the compressor comes pre wired with a socketed 80amp Heavy duty relay. Don’t be fooled this is not the same as those small part store relays. The power tabs are almost 3/8” wide. The relay has been tested for hundreds of thousands of cycles under load. The high quality contact material prevents excessive heat in the relay so the contacts will never melt into the seat making the relay stick.
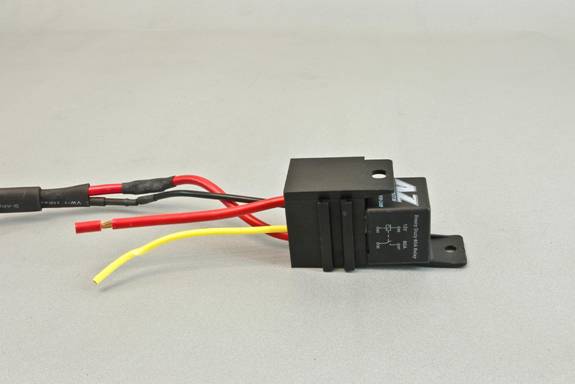
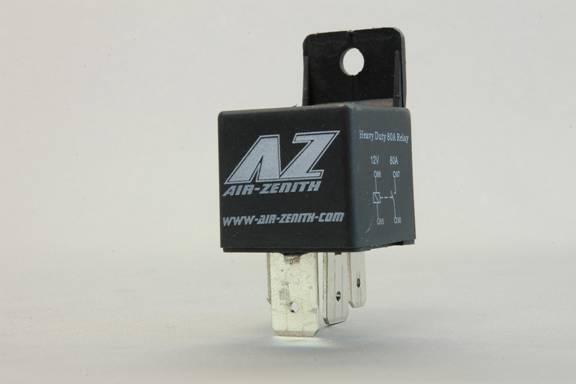
The wires are all professionally terminated and heat shrunk. An improvement over the OB1 with its bound wires in one common heat shrink tube, the OB2 now has both wires separated all the way back to the compressor to allow for a much simpler and cleaner install. Installing the compressor could not be more simple. Install the ground wire to the chassis of your truck and secure. Now take the large Positive wire and connect it to your power wire from the battery. Last connect the small switch wire to your pressure switch and you are done! Yes it is that easy.
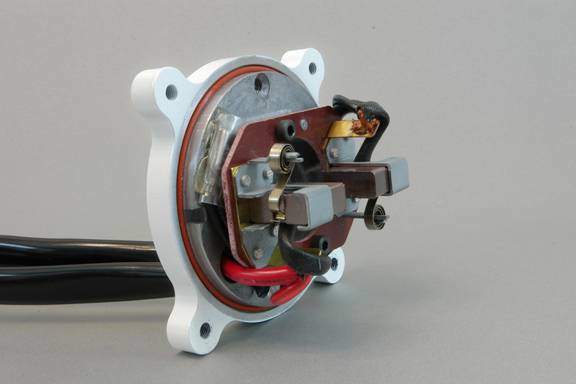
The best part the OB2 now has a built in thermal sensor. This sensor will monitor the operational temperature of the compressor and if the compressor for some reason where to over heat the thermal switch will shut off the relay thus stopping the compressor, but will keep the cooling fan running on the compressor to help it cool down faster. By having the relay shut down the compressor the thermal sensor will see no load so the sensor will last for many years. Every wire on the compressor including the cooling fan has been wrapped in braided 100% fire proof silicone wrap and heat shrunk at the ends.
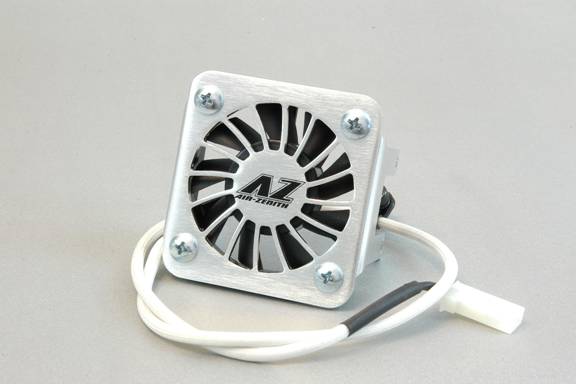
This brings me to the cooling fan. If for some reason the fan gets damaged, highly unlikely now that the fan is completely water proof and certified. The fan can be readily replaced by simply unplugging the fan from the included connector on the back of the motor and swapping it out. No more sending it back or messing with a soldering iron.
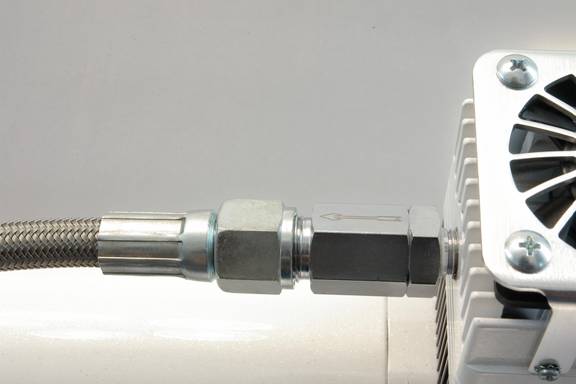
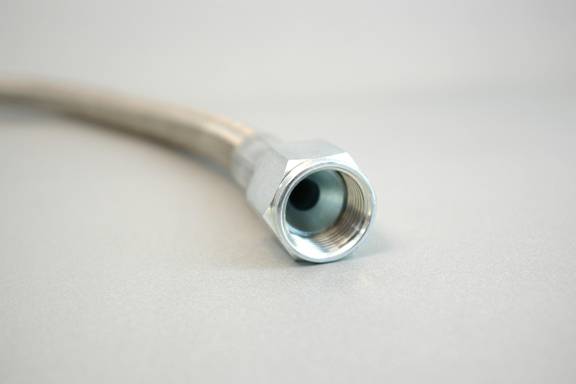
Next step on the outside is the top end. The leader hose has been doubled in size with a true PTFE liner for the ultimate in flow and reliability. The tank fitting has been upgraded from ¼” NPT to a massive ½” NPT so no more adapters are needed to thread it into most tanks. The check valve has been moved to the compressor for faster performance. Also the Check valve has been totally redesigned. Not only being twice the size, it is also fully cleanable by the end user. Simply twist it apart clean out any material that may cause it to stick and you are back on your way and working!

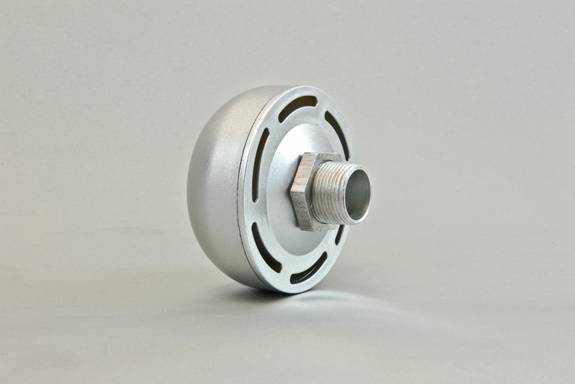
One of the largest complaints of the OB1 compressor was the failure rate of the main Piston bearing. After allot of research the problem was found to be water infiltration into the crank case and bearing. Water is a huge enemy to an air compressor it can quickly rust and corrode critical components. The way this was handled was ingenious. The filter was redesigned from the open element K&N style to the enclosed silver filter you see now. This design forces the incoming air to travel a complex passage way thus shedding the water from the air. The filter element is also now replaceable without replacing the housing. The filter has also designed into it a jam nut for securing the filter to the compressor so it can not fall off. As well this design allows the filter to be remote mounted via a bulk head union and line. This allows you to direct the air inlet to a nice clean dry place if the compressor is not in the most ideal of locations.
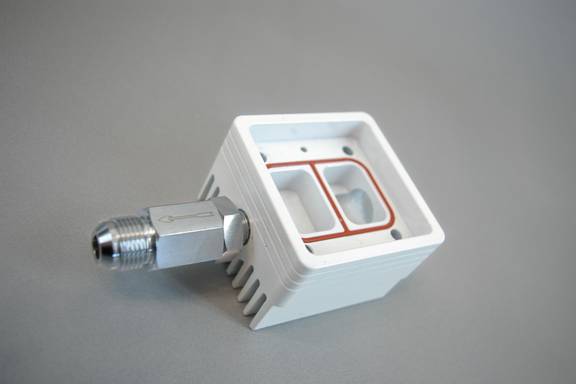
The best feature of the new filter design is the inlet has been moved from the OB1’s location on the crank case the new OB2’s location on the Head of the compressor. This helps the compressor in 2 great ways. First the nice cool inlet air is routed through the head and valve plate this helps cool the output valve as well as the head of the compressor. Second the air never enters the crank case; this means all of the bearings are sealed into a clean sealed environment in the crank case where no moisture can enter. Not to mention with the crank case no longer under vacuum dirt and moisture is no longer pulled in around the small gaps of the motor and wires allowing it to get into the motor and bearings. All of this means the compressor will run much longer and much cooler.
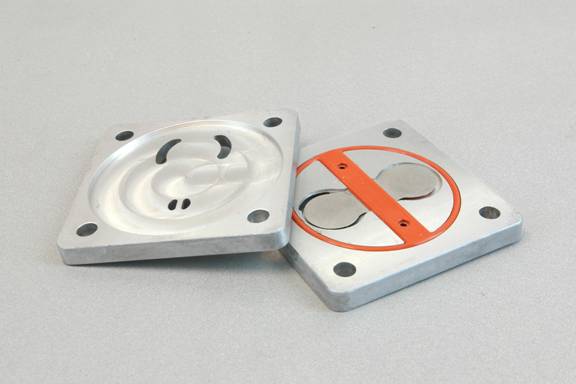
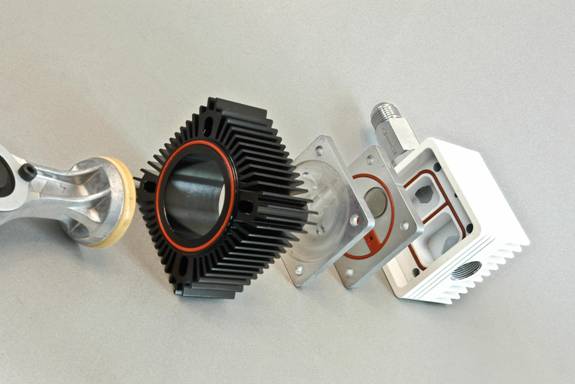
Now inside the compressor is where this unit really shines. The valve plate mentioned above is a unique design for Air Zenith it is a valve plate design this design is a smaller version of what is used in huge industrial compressors. The valves are incased between two ¼” thick aluminum plates that act as both a restraint to prevent over extension during extreme flow rates as well as prevent heat tempering of the valves from them getting too hot. The valve plate is designed in such a way that the heat is pulled from the valves and spread into the valve plate like a heat sink where the nice cool incoming air can absorb it and cool the valves. The best feature of this design is if a valve ever breaks it can not go anywhere, it is trapped in its chamber so it can not fly around damaging other expensive components in the compressor. Replacing the valves is also easier then ever. Remove the (4) Allen head bolts and lift up the valve plate and pull it apart the valves simply lift out and can be replaced. No fancy tools needed and no hardware to break or get stuck.
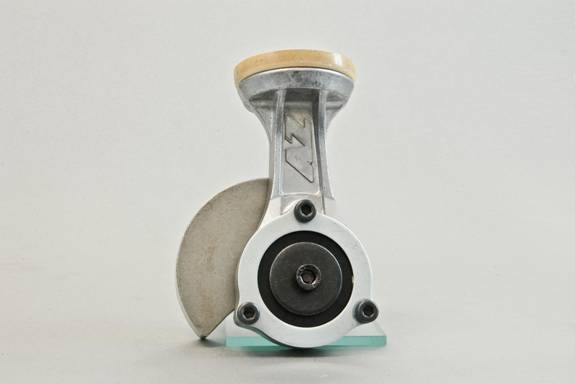
The piston and counterweight have also gone under the knife they have been beefed up big time. For the OB2 now runs at a much slower RPM then the OB1 compressor this means a much much longer life span for all of the moving components. But the OB2 is almost 2X as fast as the OB1 so this means the piston size has been increased; this means more stress on the piston. This explains why the piston is almost twice the weight of the old design. The permanently lubricated bearing in the piston has a new retention mechanism that allows for easy bearing replacement down the road. Simply remove (3) small Allen bolts and the piston comes apart and the bearing will fall out.
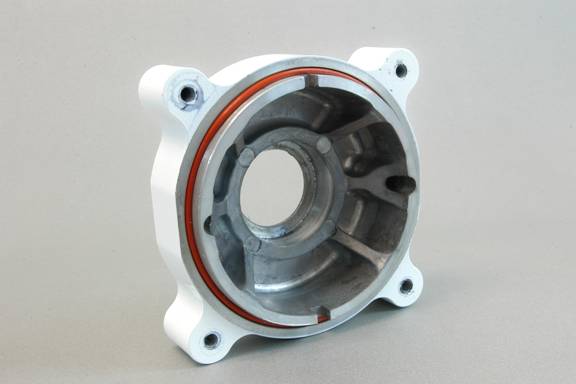
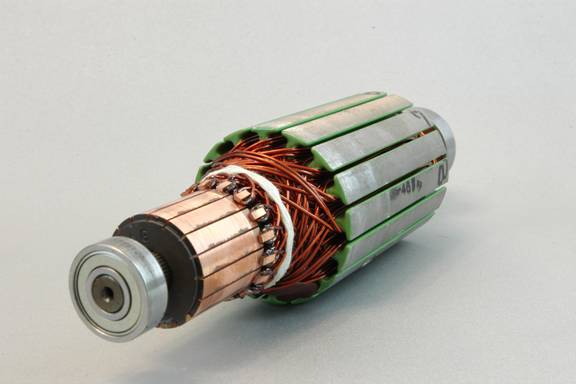
Last but most certainly not least the heart of any compressor, the motor. The motor for the OB2 is a marvel of engineering the largest highest torque motor has been designed into the smallest Package ever designed by AZ this small motor packs a 3/4HP ratting and manages to only pull a max 35amps when running at pressure! The low RPM and high torque allows for the compressor to run much cooler and quieter. There is a noticeable decrease in the noise generated by the OB2 compressor. Added to the large mass of the beefed up components allows for far less vibration then the OB1 compressor.
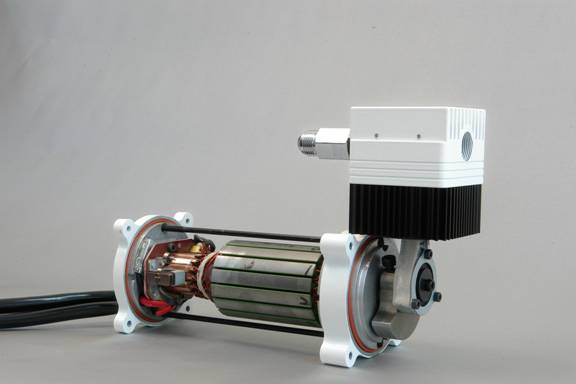
So what does this all mean? Speed performance and reliability. From the strengthened components to the redesign of how the compressor operates to the working of a new high performance motor and monitoring system. This compressor has put it place into the market as the fastest most reliable compressor ever made by Air Zenith To prove it they have backed this compressor with an unheard of 2 year warranty! Air Zenith has defiantly come back with a bang and hit the ground pumping for they are staged and ready to take the market by storm once again.
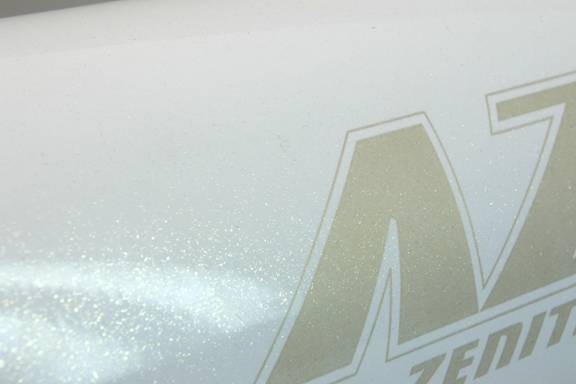
The Details:
The OB2 compressor will come in Gloss white with metal flake and Gloss black also with metal flake. The speed of the compressor is projected at 1.80CFM at 140PSI and a Max draw of 35amps.
After Extensive testing the below information was recorded.
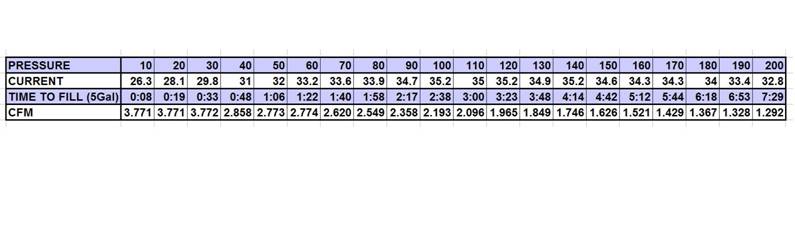
More info here,
www.air-zenith.com
Cheers,
~Doug
All information,
© 2009 DJD Laboratories Doug DeHaven